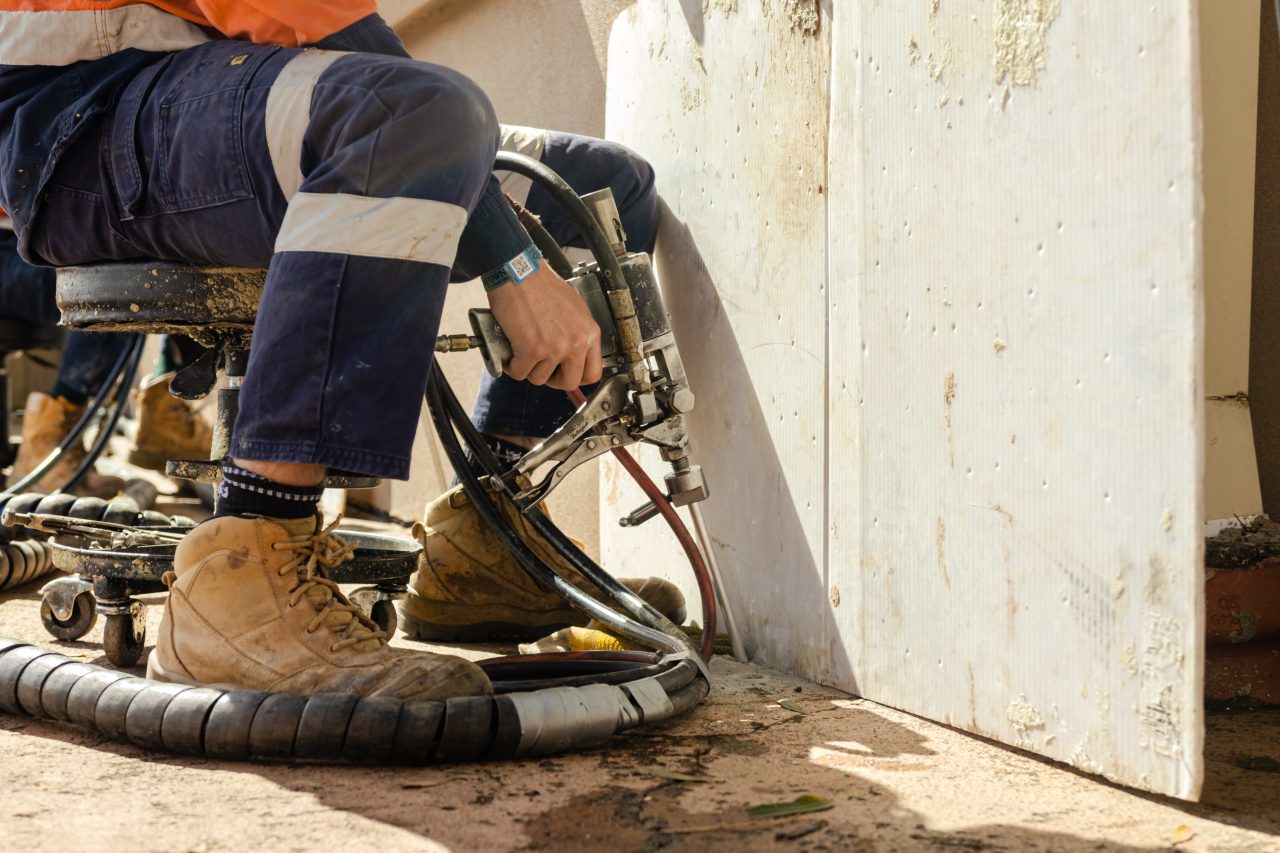
Resin Injection
Concrete Injection Repair
Concrete raising, also known as slab jacking, mud jacking, or polyjacking, is a process used to lift and level sunken or uneven concrete surfaces. Over time, concrete slabs can sink due to soil erosion, poor compaction, or natural settling. Instead of tearing out and replacing the concrete, raising techniques can restore the slab’s original height and stability in a cost-effective and efficient manner.
Ideal for various applications, from residential to commercial structures and infrastructure, concrete resin injection is a minimally invasive solution.
- 50 year product warranty
- 30+ years experience in Australia
- Non-invasive and surgical method
- Modern underpinning alternative
- Cost-effective compared to traditional methods
Video
Why Teretek® for Concrete Injection?
The Teretek® Advantage in Concrete Crack Injection
Teretek® is an exceptional choice for concrete resin injection due to its innovative and efficient technology designed to raise, re-level and re-support subsided structures. Developed by Mainmark, Teretek® employs a unique resin injection method that precisely re-levels concrete, ensuring structural integrity with minimal disruption. This non-invasive technique is highly effective for concrete crack repair, offering a swift and durable solution that significantly reduces the need for extensive excavation or demolition. Renowned for its accuracy and effectiveness, Teretek® is the go-to solution for residential and commercial applications.
Before & After Treatments
Comprehensive Solutions for Concrete Injection Repair
30,000+ Asset Owners Trust Us
Teretek® offers comprehensive solutions for concrete injection repair, adeptly handling various structural challenges. Its versatility ensures effective repair of cracks, voids and subsidence.
The transformative before-and-after results visibly demonstrate the efficacy of Teretek® in restoring and enhancing the stability and appearance of concrete structures.
Mainmark Google Reviews
Features & Benefits
Mainmark’s Solutions & Technologies
Fast
Our technologies have fast curing times and treated areas can be used immediately or without the delays compared to traditional repair methods.
Environmentally Inert
Our technologies use an inert material that is non-toxic and does not leach into the environment or affect the treated area.
Non-Invasive
Our solutions are of surgical nature compared to traditional methods.
Cost-Effective
Compared to traditional methods, our solutions are more cost-effective, with minimal disruption to the area.
Understanding the Causes of Concrete Cracks
The Underlying Reasons for Concrete Subsidence
Concrete, despite its robustness, is susceptible to cracking, which can compromise the structural integrity and aesthetics of buildings and infrastructure. Understanding the root causes of these cracks is crucial in selecting the right repair method, such as Teretek® for concrete injection.
Moreover, the impact varies depending on the type of ground involved. When the ground undergoes changes, building subsidence becomes a prevalent concern. In such cases, foundations or footings lose their support and sink due to the weakened ground.
Soil Types
Moisture levels in the soil affect reactive clays as they expand and contract.
Oversaturated clays lose their strength resulting in footing subsidence. In loosely packed soils, such as sand and silt, the fine particales in the soil can wash away causing the footing to settle.
Tree Roots
Neighbouring trees and shrubs absorb water using their roots causing movement in the soil as it soaks up moisture in the ground.
Footing Systems
Poor foundation design or inadequate compaction of soil during construction results in movement of the structure as it settles.
Excess Water
Burst or cracked water pipes including blocked sewage and rain gutters can oversaturate clay soils or wash fine particles from sand and silt soils and cause footings to subside.
Extreme or Seasonal Weather
Natural disasters such as flooding, drought and earthquakes affect soil moisture levels in particular clay resulting in excessive foundation movement.
Renovation or Construction
Vibration caused by nearby construction activity such as drilling or piling, or heavy road traffic causes soil particles to shift and settle, resulting in ground subsidence.
Projects
Featured Residential Projects
Get a quote
Arrange a site assessment in 3 simple steps:
Step 1
Submit your enquiry using our online form. Include a brief message about the type of foundation issues you are experiencing.
Step 2
Our friendly customer service team will be in touch to schedule a site assessment that suits you.
Step 3
One of the Mainmark experts will visit your home or property, assess the damage, and ascertain the likely cause. They will establish the approach needed, creating a plan specific to the needs of your building and provide you with a detailed quote.
FAQ
Frequently Asked Questions
We’ve compiled answers to some of our customers’ most common questions.
However, we understand that your situation may be unique, and you might have specific questions not covered here.
If you’re worried about subsiding concrete, call Mainmark for an obligation free expert opinion.
What is concrete injection?
Concrete injection, often employed by Mainmark, involves injecting a specially formulated resin or grout into cracks or voids within subsided concrete structures. This resin injection processs strengthens and re-levels the compromised areas, restoring the structural integrity of the concrete. Mainmark’s unique product, Teretek®, is a notable example, offering a non-invasive, efficient solution for sinking concrete repair.
How long does concrete injection last?
The longevity of concrete injection repairs, especially when using Mainmark’s Teretek® technology, is significant. These repairs are designed to be durable and long-lasting. The exact lifespan can vary based on the environment and the specific conditions of the site, but they typically offer a long-term solution, often lasting several decades.
How much does concrete injection cost?
The cost of concrete injection varies depending on several factors, such as the extent of the damage, accessibility of the crack, the type of resin used, and the size of the project. Mainmark provides customised solutions, and costs are typically calculated after a thorough assessment of the specific needs of each project. Generally, it is a cost-effective alternative to more extensive repair methods.
How do you inject concrete cracks?
Mainmark injects concrete cracks using a process that involves drilling small holes into the affected area and then injecting the resin under controlled pressure. Teretek® resin is used for its expansive properties, which fill and seal the cracks effectively. The process is precise and designed to cause minimal disruption to the surrounding area.
What is Concrete Raising?
Concrete raising, also known as slab jacking, mud jacking, or polyjacking, is a process used to lift and level sunken or uneven concrete surfaces. Over time, concrete slabs can sink due to soil erosion, poor compaction, or natural settling. Instead of tearing out and replacing the concrete, raising techniques can restore the slab’s original height and stability in a cost-effective and efficient manner.
How Does Concrete Raising Work?
The process involves injecting a lifting material beneath the slab to push it back into place. The steps generally include:
- Assessment & Preparation: Professionals inspect the sunken concrete to determine the severity of the issue and the best method to raise it.
- Drilling Holes: Small, strategically placed holes (usually ⅝ to 1 inch in diameter) are drilled into the affected slab.
- Injecting the Lifting Material: A specialized lifting material is injected into the holes to fill voids beneath the slab. The material expands or solidifies, raising the concrete back to its original level.
- Slab Leveling & Monitoring: As the material is injected, the slab gradually rises. Technicians monitor the lift to ensure precision and avoid over-raising.
- Sealing the Holes: Once the concrete is level, the drilled holes are patched with a matching material to blend with the rest of the surface.
Types of Concrete Raising Methods
There are two primary techniques used for concrete raising:
- Mudjacking (Slabjacking)
Mudjacking uses a heavy, cement-based slurry (a mixture of sand, cement, and water) that is pumped beneath the slab to lift it. This traditional method is effective for large areas but has some drawbacks:
✔ More affordable than other methods
✔ Uses natural materials
✘ Heavier material can further compact weak soil over time
✘ Takes longer to cure, typically requiring 24-48 hours before full use
- Polyjacking (Foam Lifting)
Polyjacking uses an expanding polyurethane foam instead of cement-based slurry. This modern method has several advantages over mudjacking:
✔ Lightweight material reduces soil stress
✔ Quick curing – can support weight within 15 minutes
✔ Water-resistant and durable
✔ Longer-lasting than mudjacking
✘ More expensive than mudjacking
Why Does Concrete Sink?
Several factors contribute to the sinking or uneven settling of concrete slabs:
- Soil Erosion: Water washes away soil beneath the slab, leaving empty spaces.
- Poor Soil Compaction: If the ground was not properly compacted before the concrete was poured, it can settle unevenly over time.
- Freeze-Thaw Cycles: In colder climates, the ground expands and contracts due to temperature changes, leading to shifting and sinking.
- Tree Roots & Organic Material Breakdown: As tree roots grow or buried organic material decomposes, voids can form beneath the slab.
Common Applications for Concrete Raising
Concrete raising is used for a variety of residential, commercial, and municipal applications, including:
- Driveways – Fix sunken or cracked driveways to prevent damage to vehicles.
- Sidewalks & Walkways – Eliminate tripping hazards and ensure compliance with ADA (Americans with Disabilities Act) requirements.
- Patios & Pool Decks – Maintain level outdoor surfaces for safety and aesthetics.
- Garage & Basement Floors – Prevent further structural issues caused by uneven concrete.
- Parking Lots & Roads – Restore commercial or municipal pavement without major construction.
Benefits of Concrete Raising
Cost-Effective – Typically 50-70% cheaper than full slab replacement.
Quick & Convenient – Most projects are completed in just a few hours.
Minimal Disruption – No need to remove and replace concrete, reducing downtime.
Eco-Friendly – Uses fewer resources and prevents unnecessary waste.
Prevents Further Damage – Helps avoid costly repairs caused by further sinking or cracking.
When Should You Consider Concrete Raising?
Concrete raising is a great solution if:
- Your concrete is sunken but still structurally sound.
- You notice tripping hazards on sidewalks or patios.
- Water is pooling in certain areas due to uneven slabs.
- You want a quicker, less invasive fix compared to full replacement.
However, if the concrete is severely cracked, crumbling, or has major structural issues, replacement may be a better option.
Concrete raising is an efficient, affordable, and environmentally friendly way to restore uneven or sunken concrete surfaces. Whether using mudjacking or polyjacking, this process can extend the lifespan of concrete structures and improve safety. If you’re dealing with sinking concrete, consulting with a professional can help determine the best method to fix the issue.