Sub-industry
Public Buildings
Problems
Earthquake Damage
Location
NZ
Year
2020
Solutions
Ground Improvement
Technology
Terefirm®
The problem
O’Connells, a large retail, dining and office complex in Queenstown, New Zealand, was undergoing a multi-million dollar redevelopment to revitalise the entire site, including a new external façade and internal layout modifications. O’Connells was originally opened in 1988 as Queenstown’s first major shopping centre. The new development aims to blend luxury retail with contemporary dining experiences.
As O’Connells is located in the heart of Queenstown and is an iconic local destination, the owners, Skyline Enterprises, felt it was important that the 4,000m2 building upgrade was earthquake resilient, particularly given Queenstown’s relative proximity to the Alpine Fault line.
As part of the redevelopment, a NBS (New Building Standard) rating, a seismic standard indicator that rates a building’s ability to withstand an earthquake, was set to be in the upper quartile for both the structural and geotechnical works at the complex. Therefore, a solution that would improve earthquake resilience and liquefaction mitigation was an essential requirement for the O’Connells redevelopment to achieve the desired NBS rating.
Engineers identified that the building required a new structural frame around the external perimeter and the foundations needed to be reinforced, in addition to creating a non-liquefiable crust beneath them that would mitigate the effects of excessive ground movement during an earthquake. As O’Connells consisted of 4-5 levels including a basement, undertaking the work presented significant challenges with very few feasible options available. Timing was also a crucial factor in the redevelopment. The building was closed during the works and the project needed to maintain a strict schedule in order to fit with peak trading windows.
The solution
Upon completion of the redevelopment, O’Connells needed to have an NBS score in the upper percentage quartile. This was achieved by strengthening the soil beneath the building across the entire treatment zone at a depth of 1-5 metres below the basement slab.
The Result
Mainmark’s Terefirm® Resin Injection solution was identified as the best approach for this complex project. It had already proven successful in previous liquefaction mitigation projects involving existing structures across New Zealand, including work on the Seaview Wastewater Treatment Plant in Wellington and Christchurch’s Northwood Supa Centa.
As it was imperative for the O’Connells centre to be fully operational within 18 months, time-consuming excavation work and the use of heavy machinery was ruled out. Access issues created further complications as the building’s basement was just 2.1m in height in some areas, and there was only one vehicle entrance ramp which was blocked by scaffolding. The heave tolerance on the building also required careful planning and coordination, with the basement slab, walls, and columns requiring constant monitoring throughout the ground improvement process.
To confirm the Terefirm® methodology for the site, Mainmark first conducted a 3-week ground improvement trial prior to undertaking the full scope of work. This included testing a 6m x 6m panel zone with 39 resin injection points to validate the design. Drilling small injection points at basement level, Mainmark was able to inject the expanding polyurethane resin into the soil, to a depth of 5m below the basement slab, with minimal impact on surrounding building activity and no negative effects on the existing structure. The client’s engineers therefore verified the likelihood of Terefirm® mitigating liquefaction in the event of an earthquake, allowing the building to reach the desired NBS percentage.
Mainmark commenced the project in August and completed the work 5 months later with Terefirm® successfully densifying soft sections of ground within the treatment zone. The ground improvement work was completed under budget, achieving the soil strengthening levels required. This allowed Skyline Enterprises, the developers of O’Connells, to complete the redevelopment and re-open with a stronger foundation in time for Christmas.
This successful project was the second largest Terefirm® treatment project to be completed by Mainmark, after the Seaview Wastewater Treatment Plant liquefaction mitigation project which was completed in 2019.
Skyline Enterprises general manager of developments, Steve McLean, said all dealings with Mainmark were prompt and efficient.
“Mainmark took the time to carefully explain the technical aspects of the project and provide information about past projects utilising the same approach. This was key to us then trialling their Terefirm resin injection solution. After the trial’s success, it was an easy decision for us to proceed with their product as we had proof that it would achieve the result we wanted.”
“We were impressed with Mainmark’s professionalism and accuracy and thanks to Terefirm we were able to achieve our goals for this project in terms of performance, cost and timing.”
Resources
Project Resources & Downloads
Terefirm® Resin Injection Used To Increase Liquefaction Resistance At O’Connells Shopping Complex
Download file
Please fill out this form to access this file.Next Project
Teretek® Re-levels Clifftop Home Impacted by Differential Ground Settlement
© 2025 The Mainmark group of companies. ‘Mainmark®’, ‘Terefil®’, ‘Terefirm®’ and ‘Teretek®’ are trademarks of the Mainmark group of companies.
Mainmark Ground Engineering Pty Ltd
ABN: 51 606 182 503
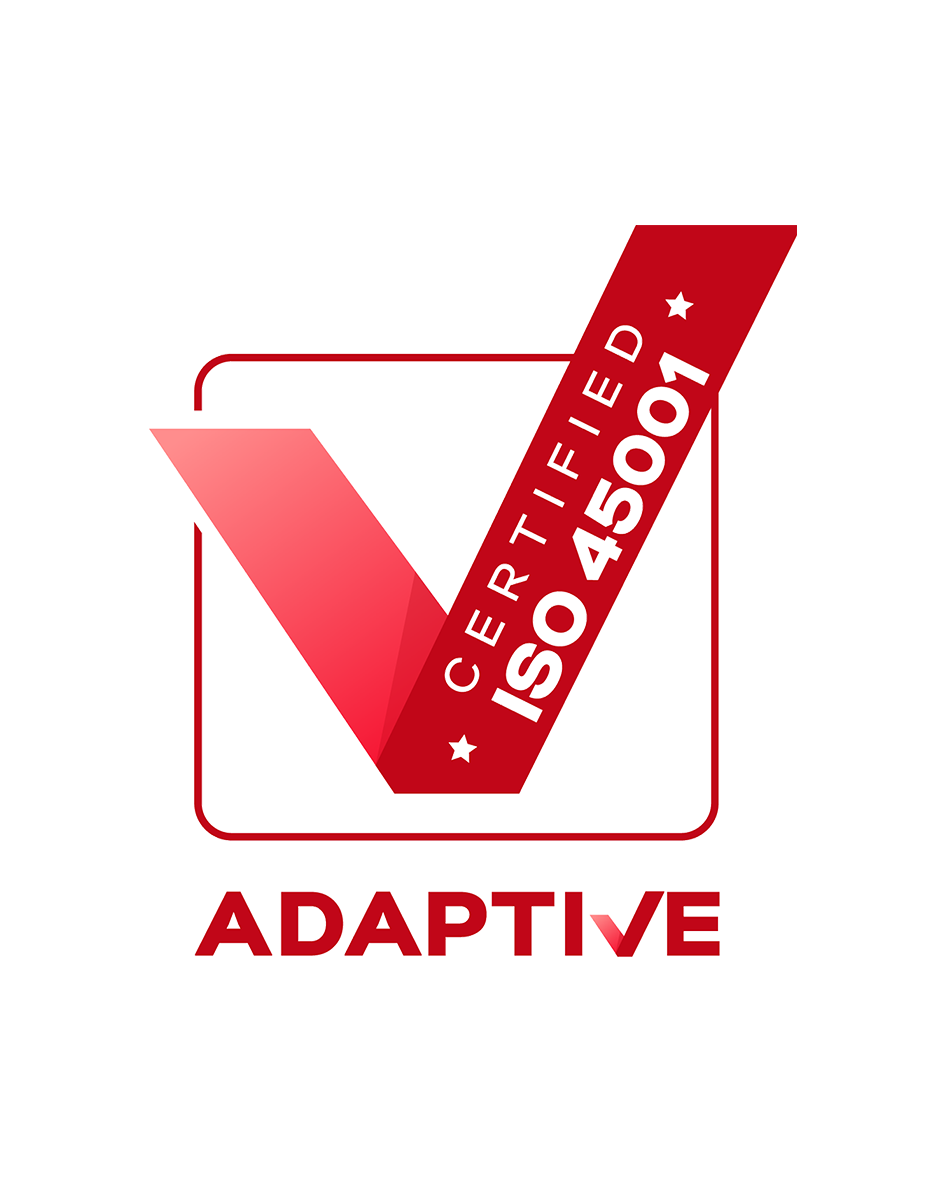
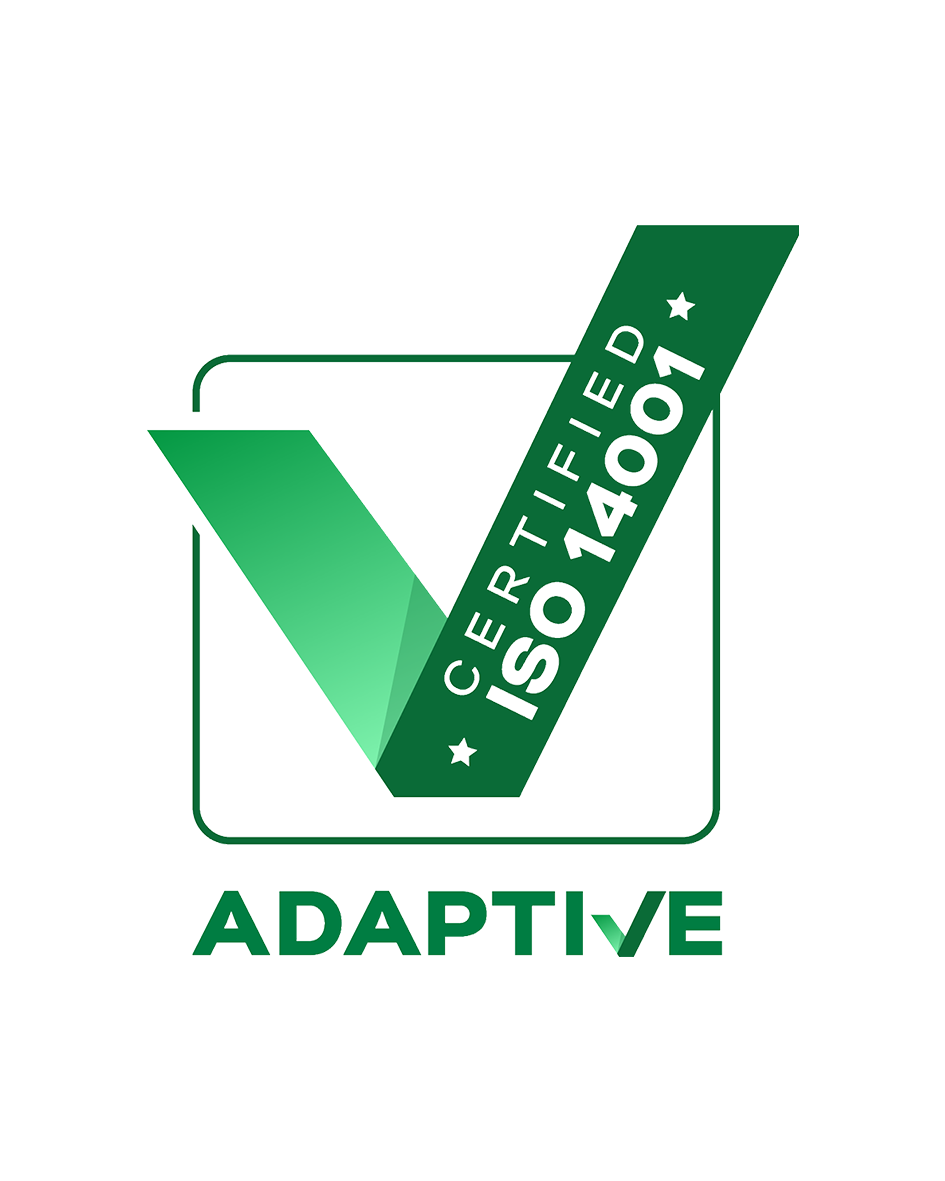
