Sub-industry
Factories & Warehouses
Problems
Out-of-level Concrete
Location
SA
Year
2020
Solutions
Slab Lifting
Technology
Teretek®
The problem
A large open paved area located at the rear of a factory in Lonsdale, South Australia, had subsided by up to 150mm. The area, also known as a hardstand, is continuously used by commercial trucks and semi-trailers to unload shipping containers and materials.
The 40m2 of affected hardstand, which was built on compacted fill, was supported by a 2m high concrete sleeper retaining wall that had been built along the rear property boundary. While the wall was reinforced with steel and concrete, it had partially rotated, with the lateral movement creating a significant gap between the top of the wall and the hardstand slab.
Subsidence had become a serious issue as water was able to flow through the crack, with the water ingress causing a washout of the soil fines and voids beneath the slab which was likely compromising the integrity of the retaining wall footings. Vibrations from constant heavy vehicle traffic was further weakening the paved concrete surface.
The retaining wall could not be reinstated as foundation correction would only further destabilise the wall and jeopardise the hardstand. It was decided to remediate the hardstand pavement to prevent it from further deterioration and limit water ingress into the fill profile. The property owner contracted Mainmark for assistance with re-levelling the hardstand area.
The solution
The property owner required a long-term solution to re-level the concrete hardstand, fill voids underneath the slab, and seal the separation crack that had formed between the hardstand’s concrete pavement and the retaining wall at the back corner of the property.
The Result
Mainmark recommended their proprietary Teretek® resin injection solution as the most appropriate technology to remediate the subsided hardstand area.
Teretek is a unique two-in-one ground improvement and re-levelling solution that is ideal for hardstands and commercial driveways, curing quickly to allow vehicles to drive over the treated area within hours.
Teretek was injected into the ground beneath the hardstand’s concrete slab at 1m and 1.5m depths, targeting the problem area in a grid-like fashion with 1.5m spacing across the surface area to ensure even distribution. The expanding polyurethane resin mix is injected through very small tubes in a process likened to keyhole surgery. On entering the ground, the components mix together and expand by chemical reaction, strengthening the ground and re-leveling the treatment area quickly with minimal disruption.
Mainmark successfully lifted the concrete slab by 152mm, which resulted in the hardstand being returned to its original position relative to the top of the retaining wall. To ensure a long-term remediation solution that would withstand ongoing movement and vibrations from heavy vehicles, water ingress needed to be reduced so a flexible sealant was specified to bridge the gap between the pavement and retaining wall.
Teretek’s non-invasive application process reduced the impact on business operations with the project being completed in a single day, on time and on budget.
Stuart Booth from Watersmeet Pty Ltd, which owns and manages the property and leases it out for commercial use, was suitably impressed with the degree of slab correction. “Mainmark’s technicians provided excellent service and expertise. Their solution was a significantly more affordable alternative to rectifying the issue, which would have otherwise required digging out the old foundations and pouring new concrete. We were amazed at how quickly the project was completed.”
Resources
Project Resources & Downloads
Re-levels Concrete Hardstand Affected by Subsidence and Water Ingress
Teretek®
Download file
Please fill out this form to access this file.Next Project
Teretek® Preserves Foundations of Large Heritage Listed Building
© 2025 The Mainmark group of companies. ‘Mainmark®’, ‘Terefil®’, ‘Terefirm®’ and ‘Teretek®’ are trademarks of the Mainmark group of companies.
Mainmark Ground Engineering Pty Ltd
ABN: 51 606 182 503
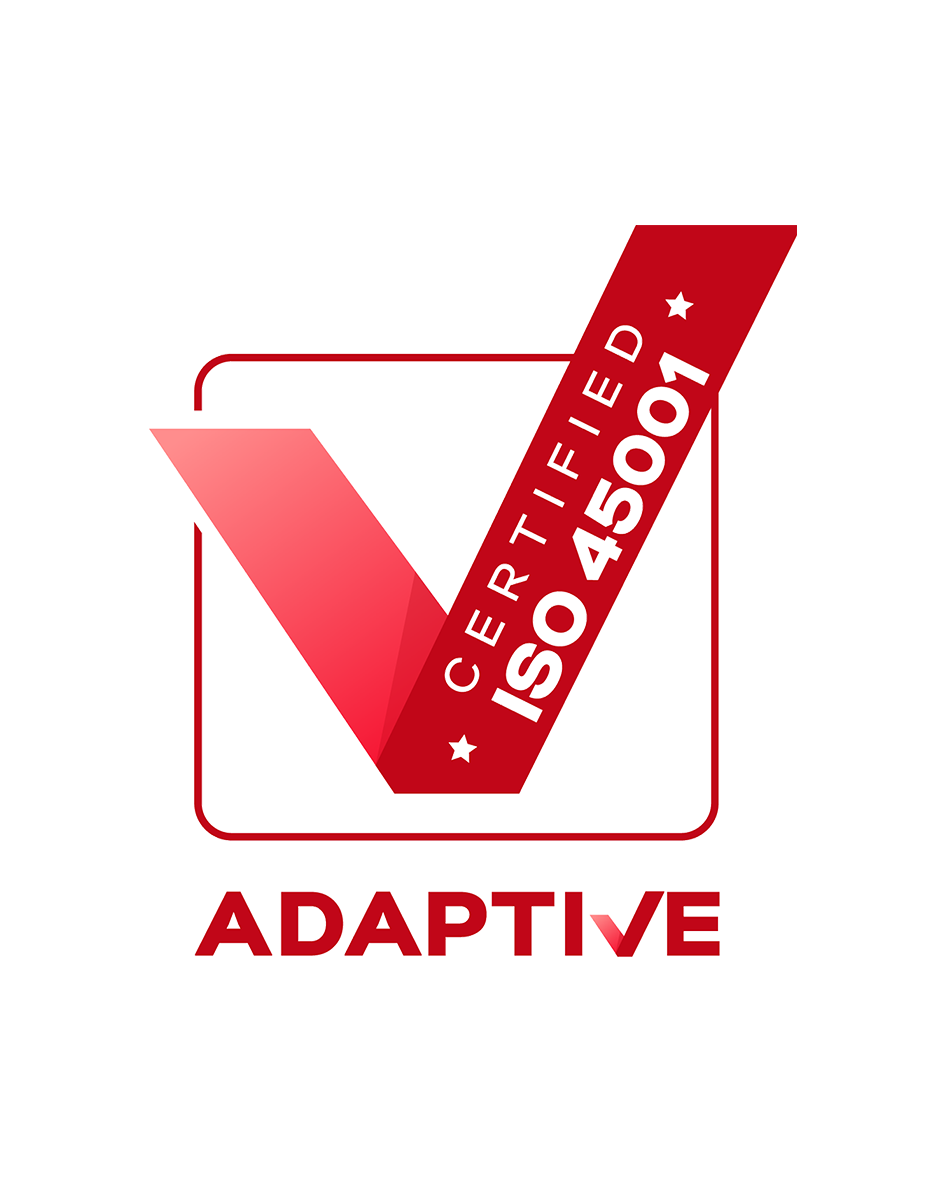
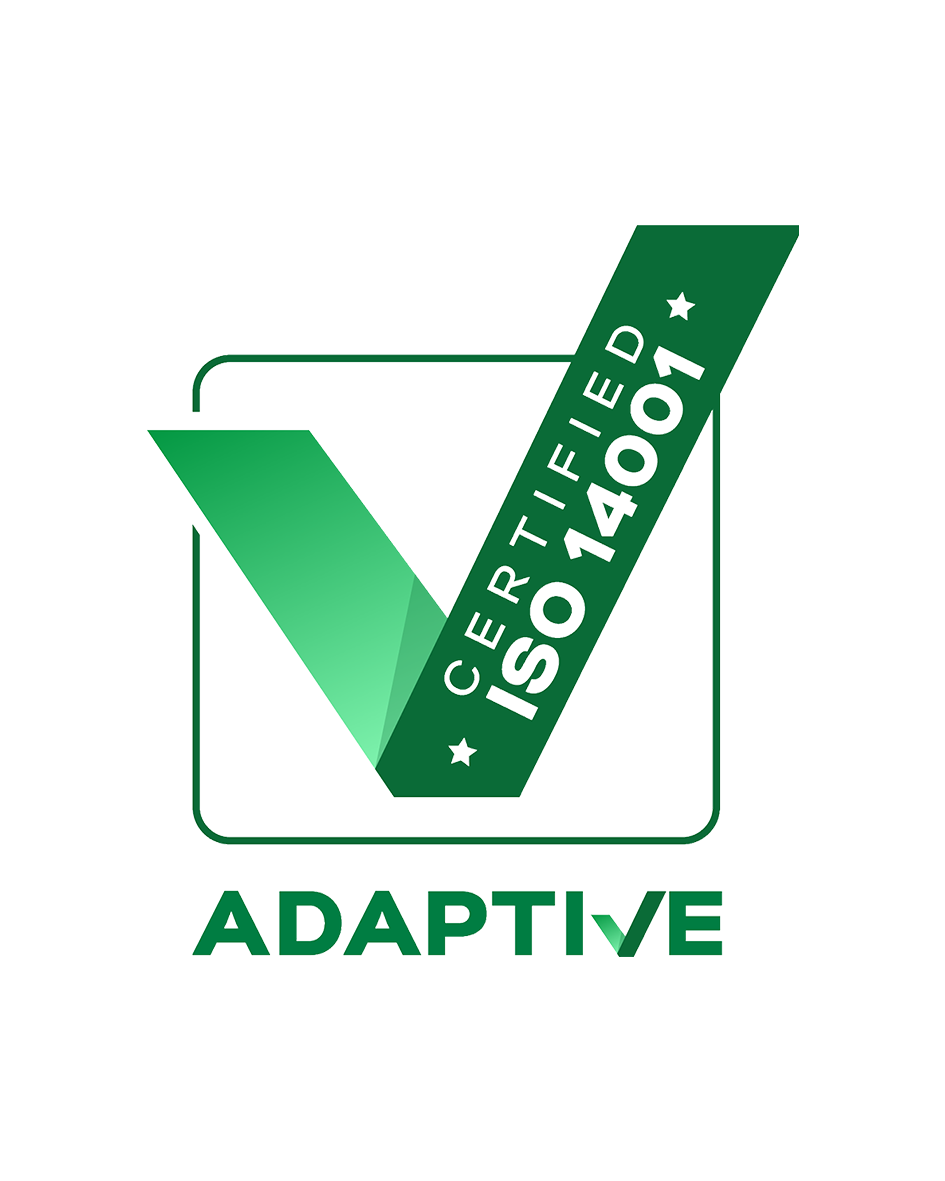
