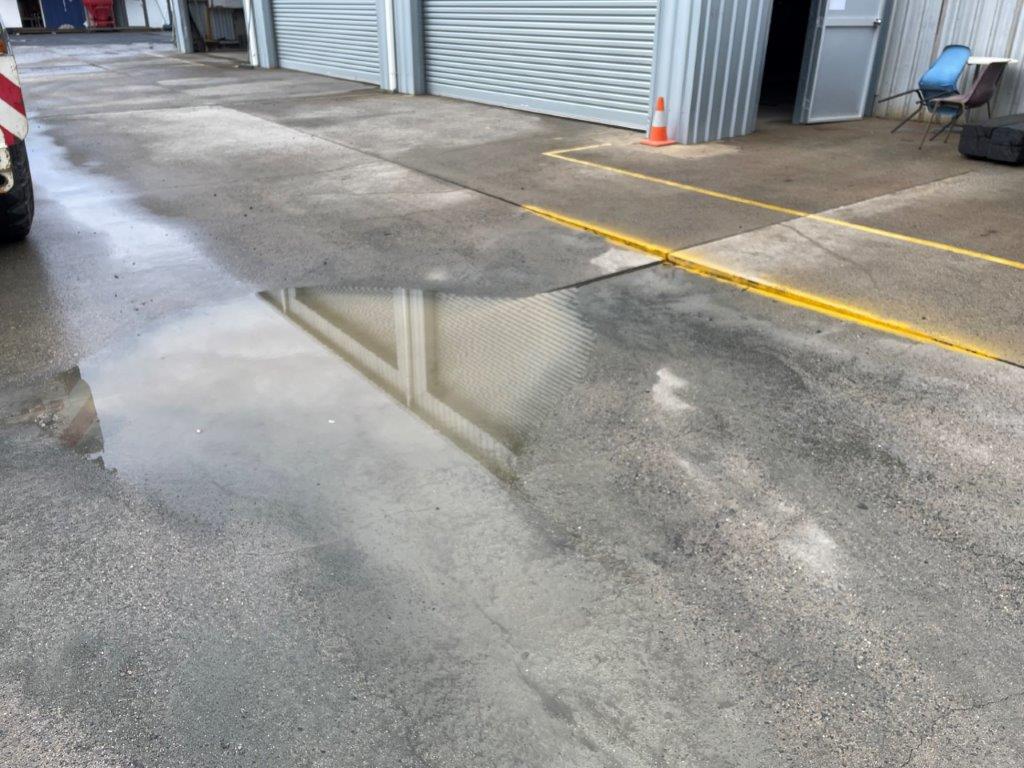
Overview
Bespoke solutions for slab lifting, slab jacking and concrete re-levelling.
Our level correction methods can cater to any building size, from airport runways and container yards to warehouses and transport yards are non-invasive, cost-effective, time-efficient, with minimal disruption to the occupants.
Sunken or un-level slabs and hardstand surfaces in warehouses or logistics environments can be a sign of foundation ground subsidence. Importantly, they can be a trip hazard, particularly if they cause water to pool in certain areas, further increasing the risk of slips and falls for your employees.
If the area is a hardstand for plant and equipment, uneven floors can result in machinery becoming un-level or misaligned. This can create significant issues around machine maintenance and performance; some sensitive machines can start producing faulty outputs and it could even void the machine’s warranty.
These un-level surfaces usually indicate soil subsidence underneath, which can deteriorate further and cause expensive, hard-to-fix damage to buildings and other structures. Even an un-level driveway at a commercial premises left untreated for too long, can become fragmented and unsalvageable.
It’s essential to fix these problems as soon as possible to prevent further damage and potential hazards.
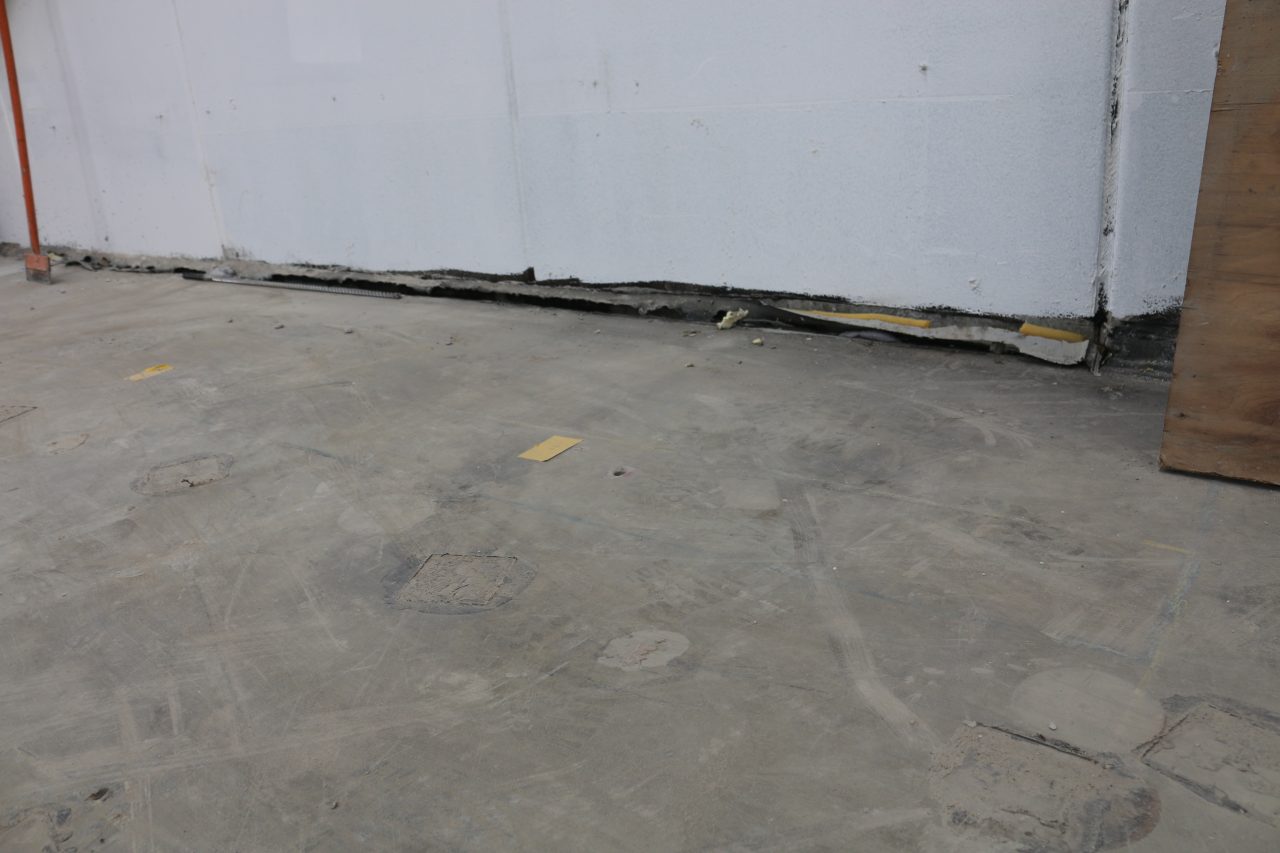
What causes slabs to sink?
Overtime, as the ground beneath slabs compresses or expends due to changes in ground moisture levels, the weighted concrete slab above will start to subside at different points.
There are many different causes of sinking slabs, including extreme weather conditions that cause reactive clay soil to contract or expand, high trafficked areas where excess weight and movement loosens sandy or fine particle soil beneath, ponding slab where excess water was used to cure concrete in small areas, nearby excavations that cause the ground to vibrate, poorly compacted soil during the construction of the building and incomplete or inadequate foundations or footings.
Common indicators of an un-level slab are misaligned joints between slab panels and soil being pushed out as weight crosses across the slab. If left untreated the lack of support under the panel can cause slab cracking and uneven surfaces.
Video
Slab Lifting In Action
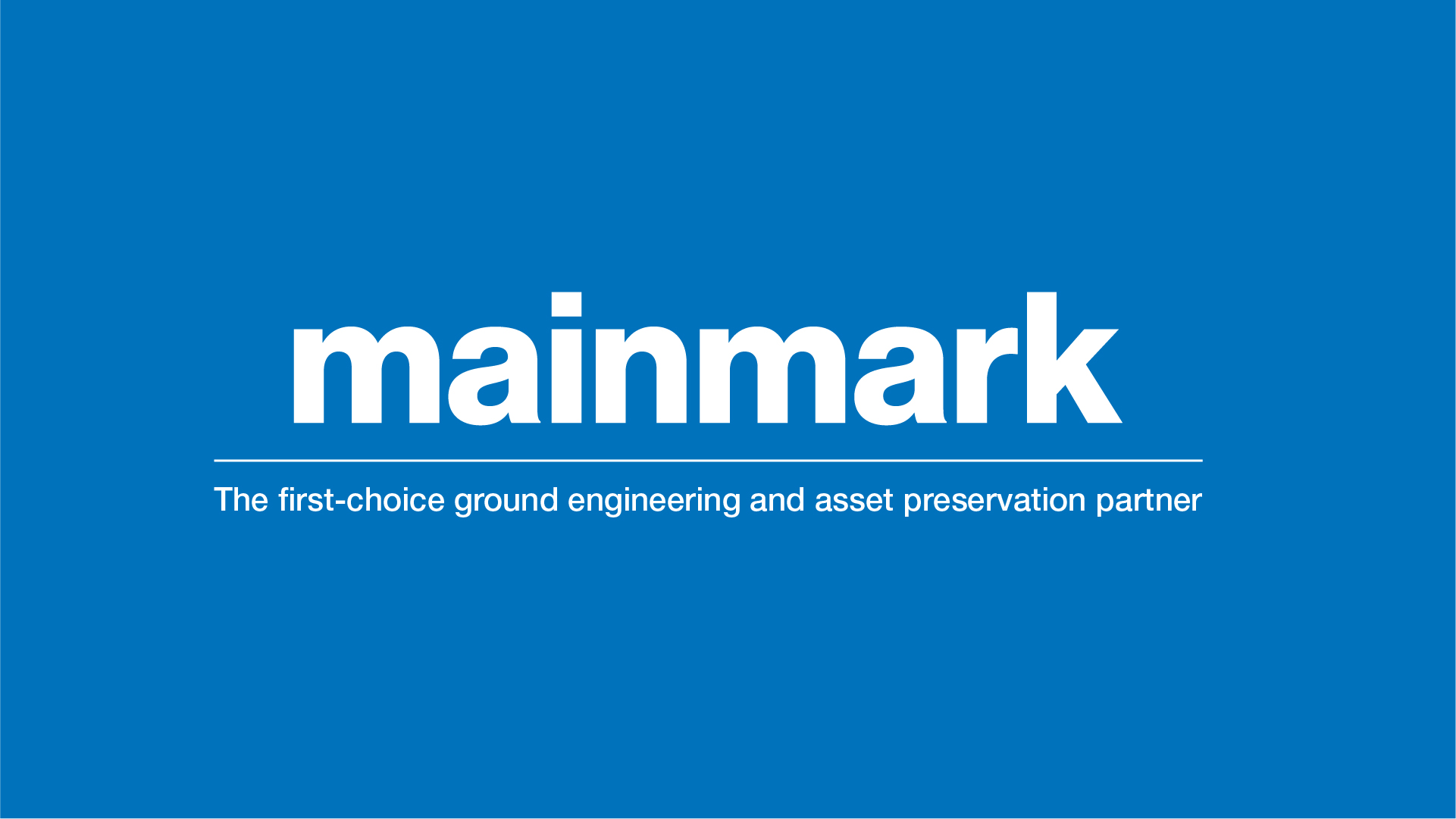
Features & Benefits
Slab Jacking Solutions
Fast
Correction with Teretek® Resin Injection can be completed within just a few hours rather than days.
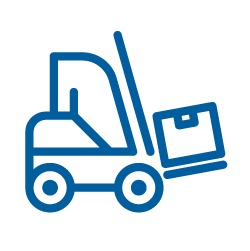
Immediately Trafficable
As soon as the repair is completed, the area can be re-opened to traffic and full use.
Non-Invasive
Repairs are performed without the need for excavation, extensive disruption.
Cost-Effective
Compared to traditional methods, our solutions are more cost-effective.
Projects
Featured Projects
Get a quote
Arrange a site assessment in 3 simple steps:
Step 1
Submit your enquiry using our online form. Include a brief message about the type of foundation issues you are experiencing.
Step 2
Our friendly customer service team will be in touch to schedule a site assessment that suits you.
Step 3
One of the Mainmark experts will visit your commercial property, assess the damage, and ascertain the likely cause. They will establish the approach needed, creating a plan specific to the needs of your building and provide you with a detailed quote.
© 2025 The Mainmark group of companies. ‘Mainmark®’, ‘Terefil®’, ‘Terefirm®’ and ‘Teretek®’ are trademarks of the Mainmark group of companies.
Mainmark Ground Engineering Pty Ltd
ABN: 51 606 182 503
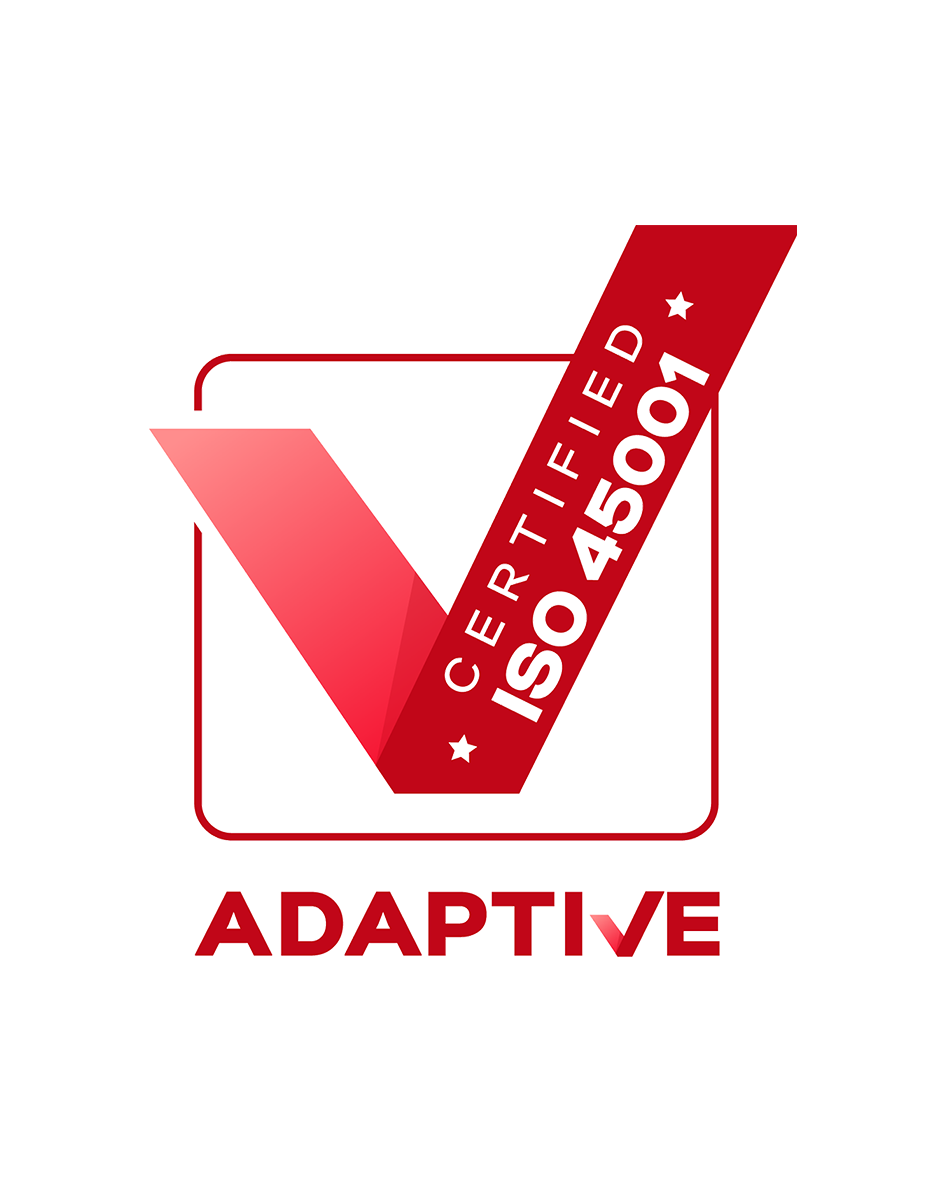
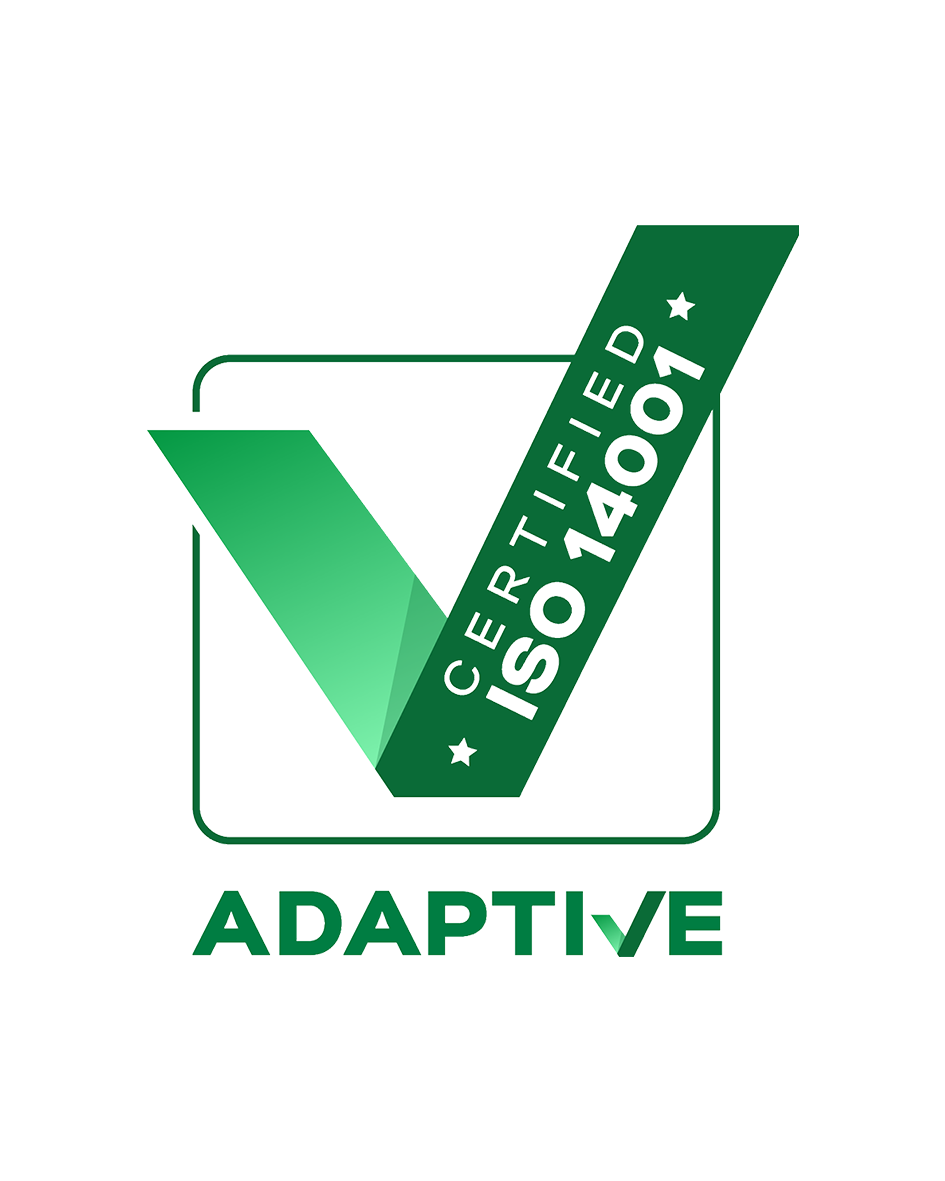
