What is Slab Jacking?
Slab jacking, also known as mud jacking or concrete lifting, is a process used to raise and level sunken or uneven concrete surfaces. Over time, concrete slabs can settle due to soil erosion, poor compaction, water infiltration, or natural ground movement. Instead of tearing out and replacing the entire slab, slab jacking offers a faster, more cost-effective solution by lifting the existing concrete back into place. This technique is commonly used to repair sunken concrete slabs including warehouse and factory floors, transport yards, driveways and garage floors.
The slab jacking process involves injecting a material beneath the sunken concrete to fill voids and lift the slab. Here’s a step-by-step breakdown of how it works:
The Slab Jacking Process
1. Assessment of the Damage
A professional evaluates the extent of the sinking and determines whether slab jacking is the right solution. If the slab is severely cracked or deteriorated, replacement might be necessary instead.
2. Drilling Access Holes
Small holes (typically 1 to 2 inches in diameter) are drilled into the affected concrete slab at strategic locations. These holes allow the injection of the lifting material.
3. The Injection Process
Polyurethane foam is pumped into the drilled holes. This material spreads beneath the slab, filling voids and compacting loose soil.
4. Slab Lift
As the injected material expands or solidifies, it gradually lifts the slab back to its original level. The process is carefully controlled to ensure even lifting and prevent further damage.
5. Sealing the Holes
Once the slab has been successfully raised and re-levelled, the drilled holes are patched to restore the surface’s appearance.
6. The Treated Area is Immediately Trafficable
The treated area is immediately trafficable and ready for full use as soon as the repairs are carried out.
Common Applications of Slab Jacking
Slab jacking, also known as concrete lifting or mud jacking, is a technique used to raise and re-level sunken concrete surfaces.
Here are some of the surfaces that can be fixed using slab jacking:
Industrial and Commercial Floors
Large warehouses or industrial buildings often experience slab settling due to heavy loads. Slab jacking can help maintain safety and operational efficiency.
Entrance Ramps
Ramps leading into buildings need to be level for accessibility. Slab jacking can correct unevenness to comply with safety regulations.
Driveways
Prevents tripping hazards and improves curb appeal.
Sidewalks and Walkways
Ensures pedestrian safety by levelling uneven surfaces.
Garage and Basement Floors
Sunken garage floors can lead to water accumulation and may affect vehicle safety. Re-levelling the concrete prevents these issues.
If basement floors begin to sag or settle, slab jacking can address uneven concrete, preventing further damage and enhancing structural integrity.
Mud Jacking
The traditional method
Made of cement, sand, and limestone-based additives.
|
Heavier material, which can help stabilise loose soil.
|
Takes longer to cure (usually 24–48 hours).
|
Requires larger drill holes (1–2 inches).
|
Polyurethane Resin Injection
The modern alternative
Tiny holes– Teretek is applied through keyholes, typically 6mm to 16mm in diameter.
|
Clean and quiet – The process is clean and quiet, has minimal impact on residents.
|
Resin injection – The resin injects into the ground and expands in the ground within minutes.
|
Curing time – 30 minutes. You can even use the building during the process.
|

Slab Jacking vs Concrete Replacement
Which One is Right?
Slab jacking is a great solution if the concrete is structurally sound but has settled due to soil movement. However, it may not be the best option in the following cases:
- Severely Cracked or Crumbling Concrete – If the slab is badly damaged, it’s better to replace it.
- Poor Drainage Issues – If water is causing continuous erosion under the slab, the root cause must be fixed first.
- Heavy Foundation Issues – Slab jacking is unsuitable for major foundation failures.

How Much Does Slab Jacking Cost?
Which One is Right?
The cost of slab jacking depends on factors like the extent of settling, the size of the area, and the material used. For comparison, complete concrete replacement typically is more expensive and disruptive, making slab jacking the more budget-friendly choice in most cases.
Slab jacking is an effective, affordable, and minimally invasive method to fix sunken concrete. Whether you choose traditional mudjacking or modern polyurethane foam lifting, it’s a great alternative to costly slab replacement. If you’re dealing with uneven concrete, it’s worth consulting a professional to see if slab jacking is the right solution for you.
Mainmark offer concrete slab lifting and slab jacking in the following locations. NSW, Sydney, Newcastle, Melbourne, Victoria, Tasmania, Adelaide, SouthAustralia, Queensland, Brisbane, Townsville, Perth and Western Australia.
Mainmark also provide the following in Australia: wall crack repairs, sinking floor repair, Concrete slab repair, sinking foundation repair, underpinning, ground improvement, re-levelling, subsidence repair, void filling and slab lifting
Features & Benefits
Slab Jacking Solutions
Fast
Correction with Teretek® Resin Injection can be completed within just a few hours rather than days.
Immediately Trafficable
As soon as the repair is completed, the area can be re-opened to traffic and full use.
Non-Invasive
Repairs are performed without the need for excavation, extensive disruption.
Cost-Effective
Compared to traditional methods, our solutions are more cost-effective.
Get a FREE quote
Arrange a site assessment in 3 simple steps:
Step 1
Submit your enquiry using our online form. Include a brief message about the type of foundation issues you are experiencing.
Step 2
Our friendly customer service team will be in touch to schedule a site assessment that suits you.
Step 3
One of the Mainmark experts will visit your home or property, assess the damage, and ascertain the likely cause. They will establish the approach needed, creating a plan specific to the needs of your building and provide you with a detailed quote.
© 2025 The Mainmark group of companies. ‘Mainmark®’, ‘Terefil®’, ‘Terefirm®’ and ‘Teretek®’ are trademarks of the Mainmark group of companies.
Mainmark Ground Engineering Pty Ltd
ABN: 51 606 182 503
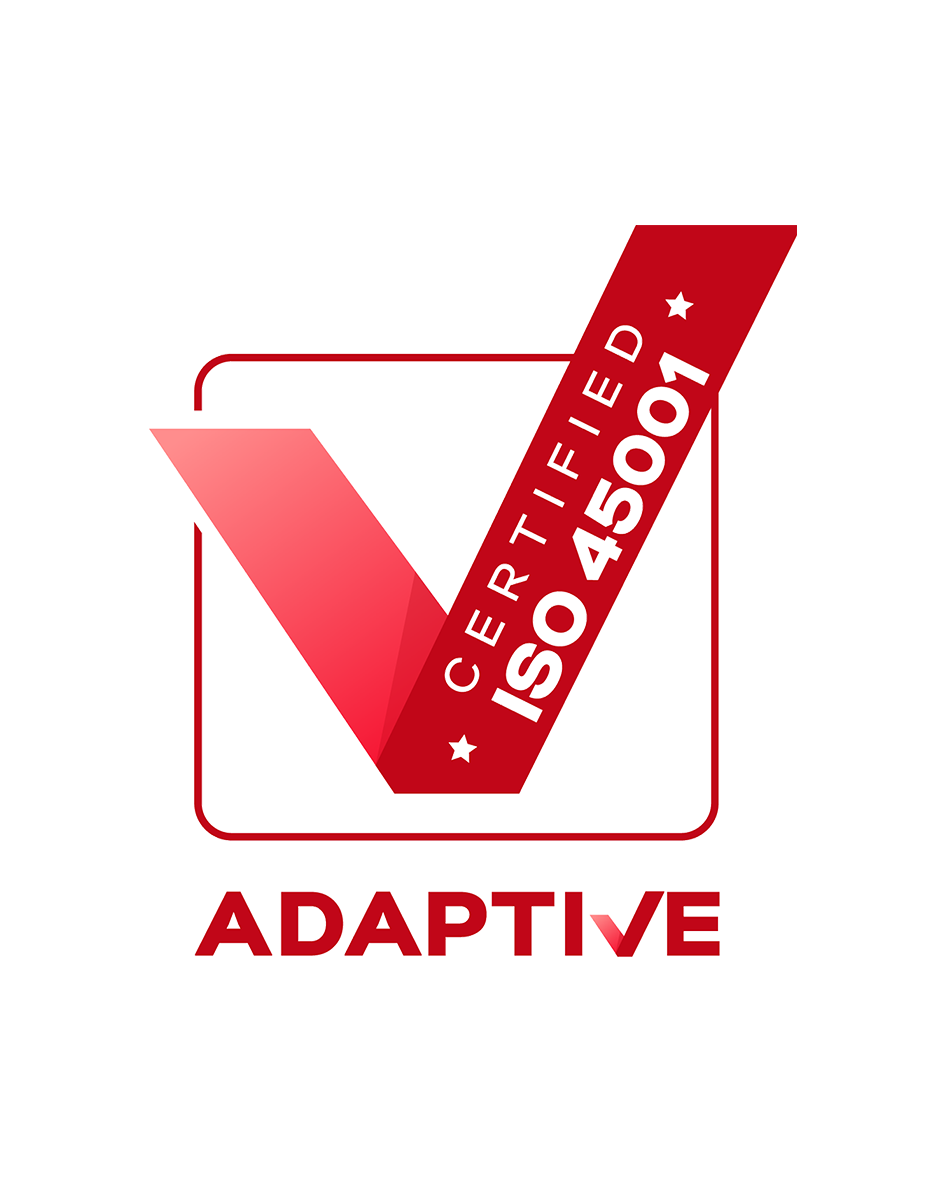
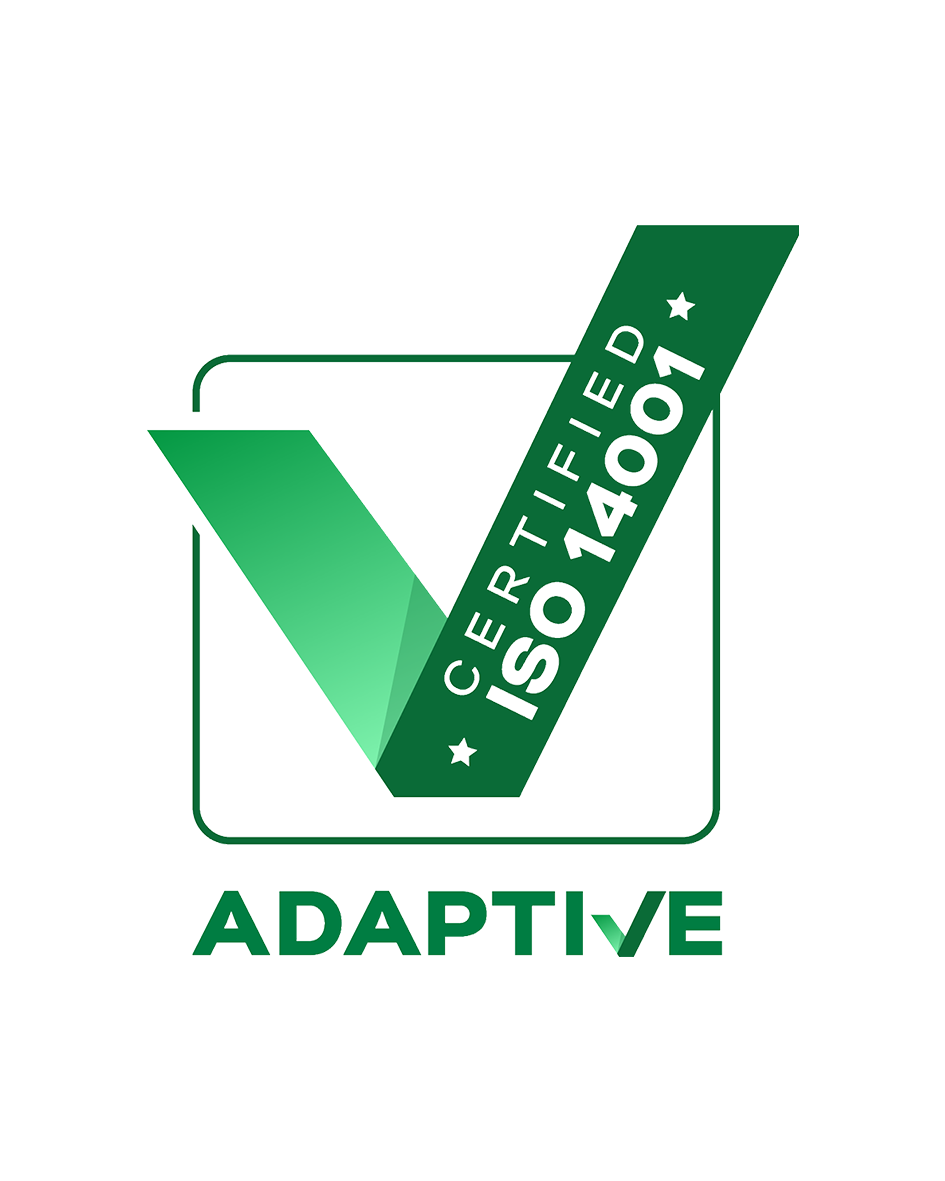
