Slab lifting and slab jacking are highly effective solutions for repairing and re-levelling uneven concrete floors in warehouses. These spaces are subjected to heavy machinery, high loads, and constant activity, which can lead to cracking, sinking, or uneven floors.
What is Slab Lifting and Slab Jacking?
Slab lifting (also known as slab jacking, mud jacking, or concrete levelling) is a process used to raise and stabilize sunken or uneven concrete slabs. It involves injecting a material beneath the slab to fill voids, improve the ground, and restore the slab to its original level.
Common materials:
- Mudjacking: A mix of sand, cement, and water, offering a cost-effective option.
- Polyurethane Resin: Lightweight, durable, and fast-curing, ideal for heavy-duty applications like warehouse flooring.

Why is Slab Lifting Critical for Warehouses?
- Operational Efficiency: Uneven floors can slow operations, disrupt workflows, and damage equipment.
- Worker Safety: Level surfaces minimize tripping hazards, protecting workers and equipment operators.
- Equipment Longevity: Uneven floors can lead to wear and tear on forklifts, pallet jacks, and other machinery, increasing maintenance costs.
- Cost-Effectiveness: Slab lifting is faster and more economical than replacing concrete slabs, reducing downtime.
- Preventative Maintenance: Stabilizing slabs prevents further structural issues, such as foundation damage or misaligned racking systems.
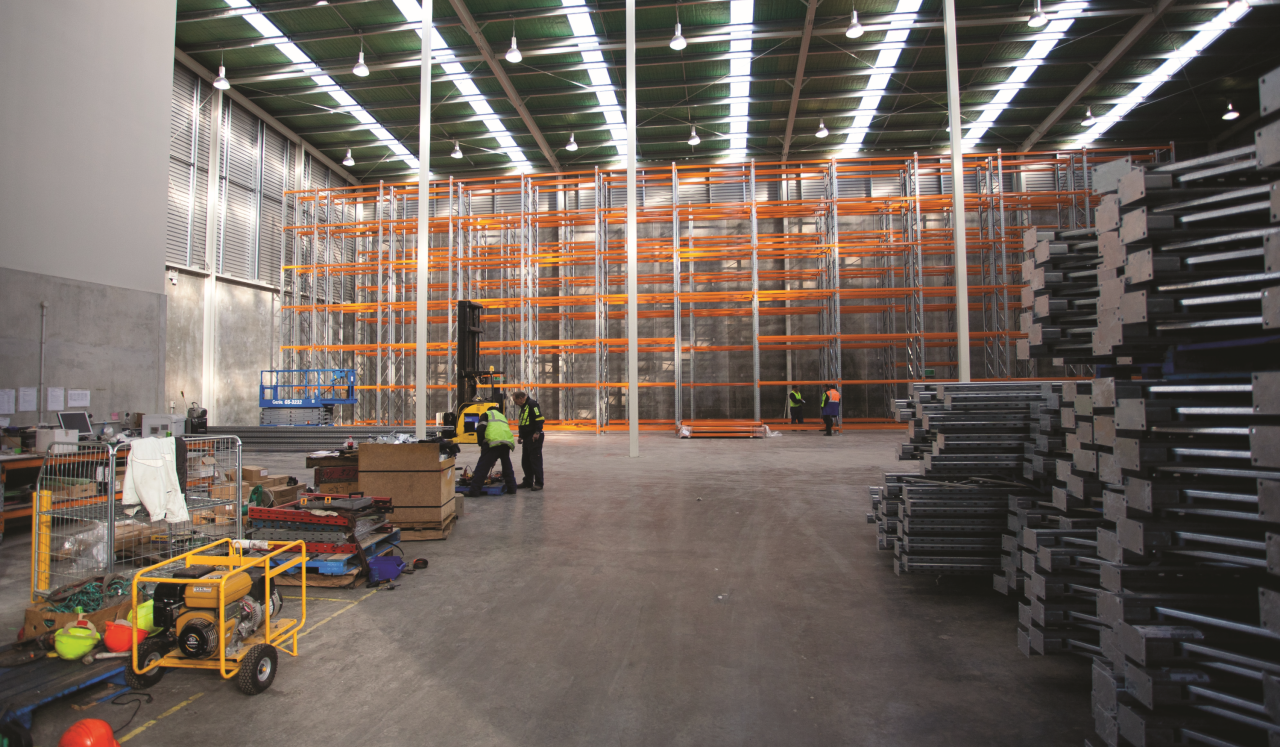
Applications of Slab Lifting in Warehouses
Forklift Pathways: High-traffic areas where forklifts frequently pass can develop sinking or cracks.
Storage Zones: Heavy pallet loads can cause settlement and uneven floors in storage areas.
Loading Docks: Areas exposed to repetitive loading and unloading often experience slab movement.
Walkways and Aisles: Keeps paths smooth and safe for workers and equipment.
Transport Yards: Re-levelling surfaces in transport yards where trucks and trailers maneuver, preventing potholes and ensuring smooth transitions to loading areas.
Car Parks: Lifting and re-levelling slab surfaces in car parks to eliminate uneven surfaces, improve aesthetics, and enhance safety for vehicles and pedestrians.
Slab Lifting Process
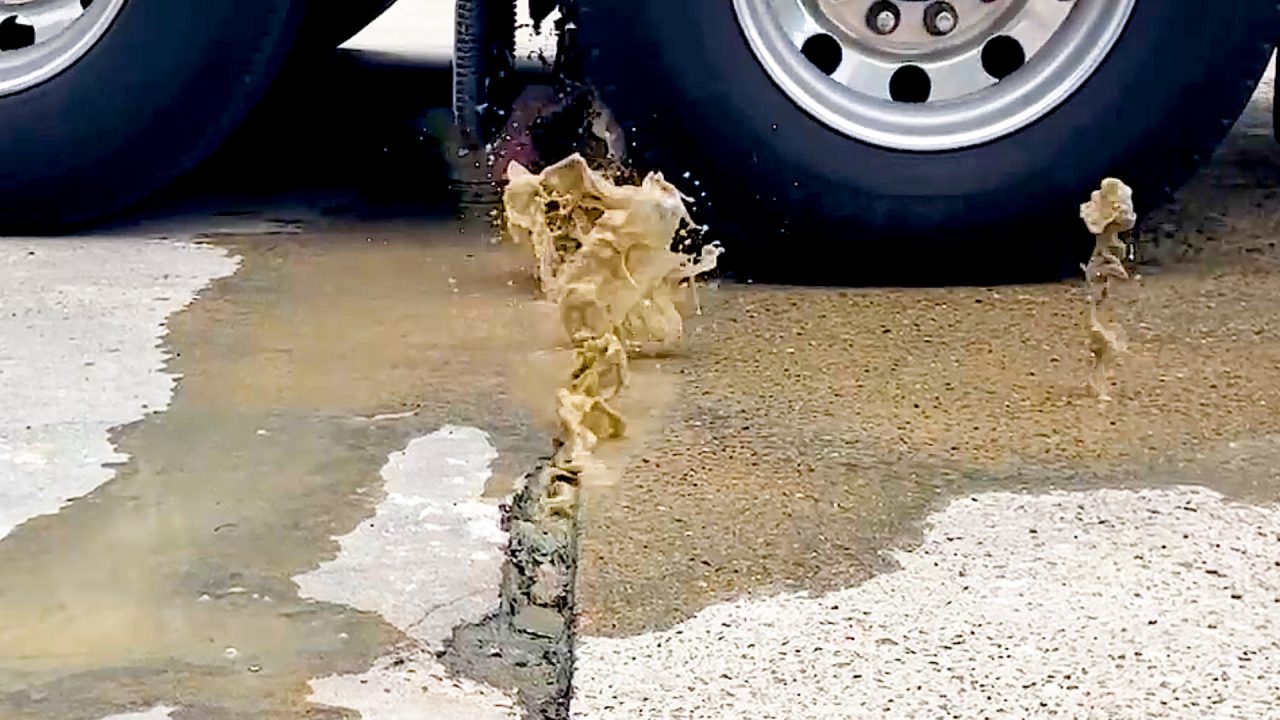
Signs Your Warehouse Needs Slab Lifting
- Cracks or gaps in the concrete floor.
- Uneven surfaces causing instability for racks, shelves, or equipment.
- Pooled water in low spots.
- Forklifts or carts struggle to move smoothly across the floor.
- Doors or equipment misaligned due to floor settlement.
Features & Benefits
Mainmark’s Solutions & Technologies
Fast
Our technologies have fast curing times and treated areas can be used immediately or without the delays compared to traditional repair methods.
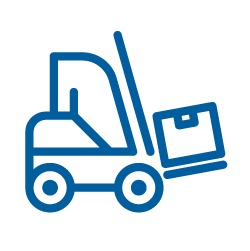
Immediately Trafficable
As soon as the repair is completed, the area can be re-opened to traffic and full use.
Non-Invasive
Repairs are performed without the need for excavation, extensive disruption.
Cost-Effective
Compared to traditional methods, our solutions are more cost-effective.
Slab Lifting – Warehouses & Distribution
Download file
Please fill out this form to access this file.Get a quote
Arrange a site assessment in 3 simple steps:
Step 1
Submit your enquiry using our online form. Include a brief message about the type of problem you are experiencing.
Step 2
One of our expert team members will be in touch to schedule a site inspection that suits you.
© 2025 The Mainmark group of companies. ‘Mainmark®’, ‘Terefil®’, ‘Terefirm®’ and ‘Teretek®’ are trademarks of the Mainmark group of companies.
Mainmark Ground Engineering Pty Ltd
ABN: 51 606 182 503
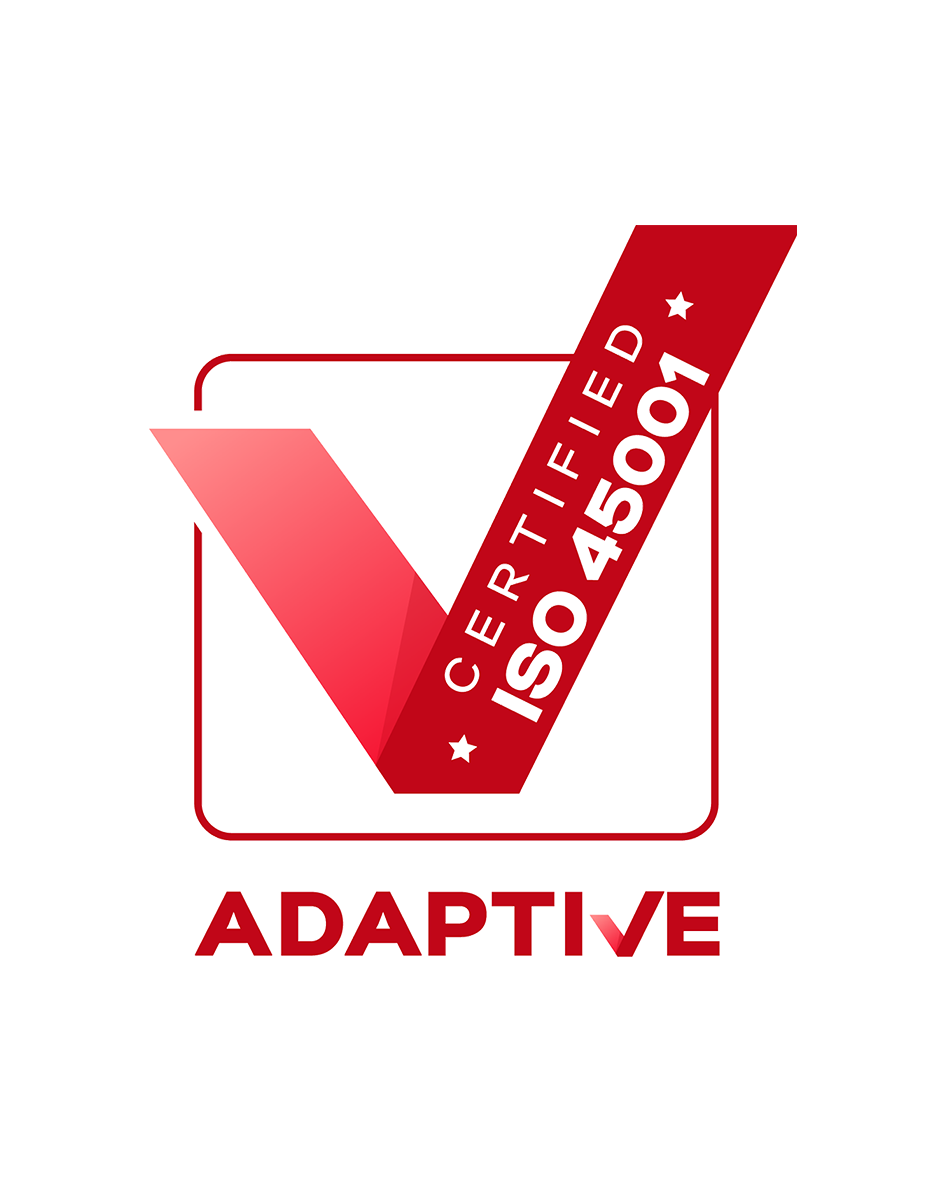
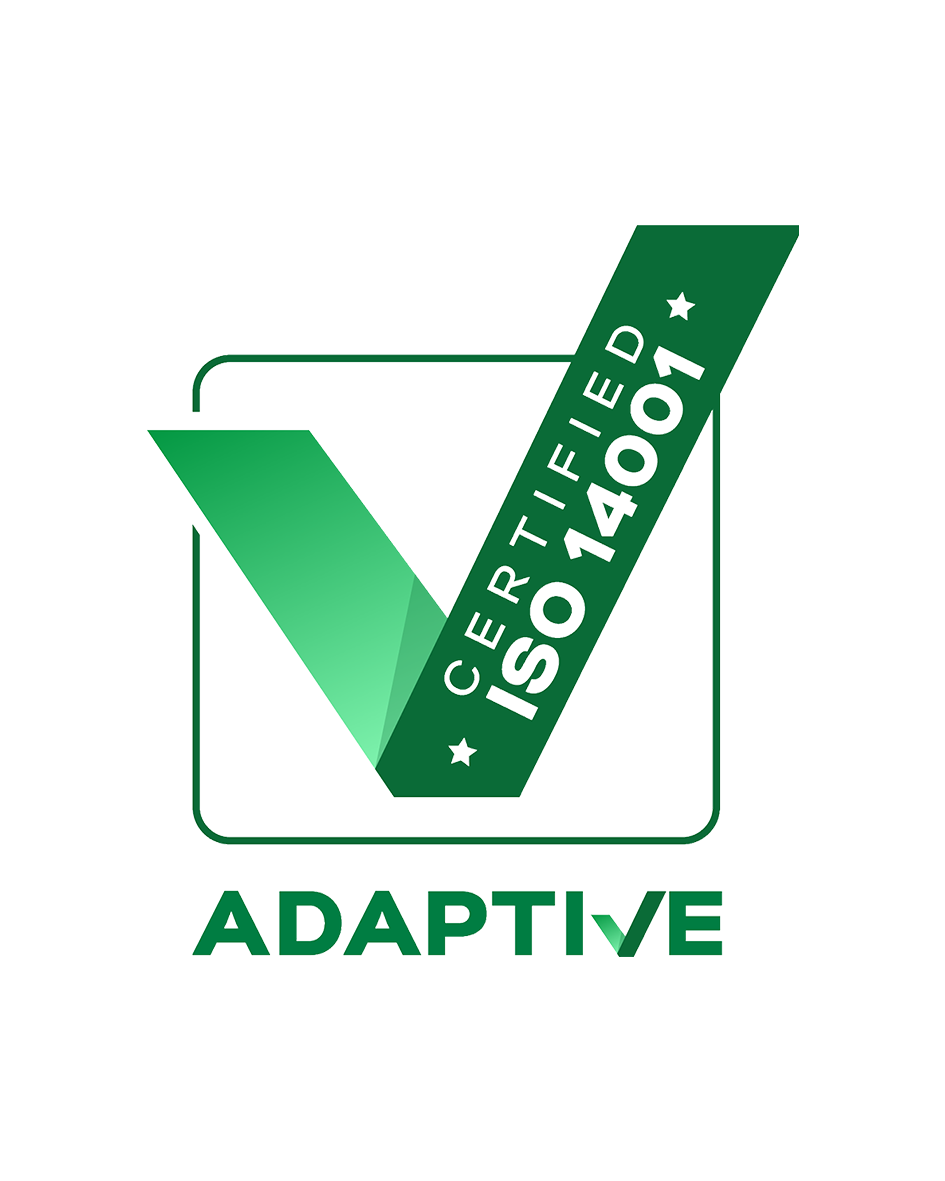
