Resin Injection
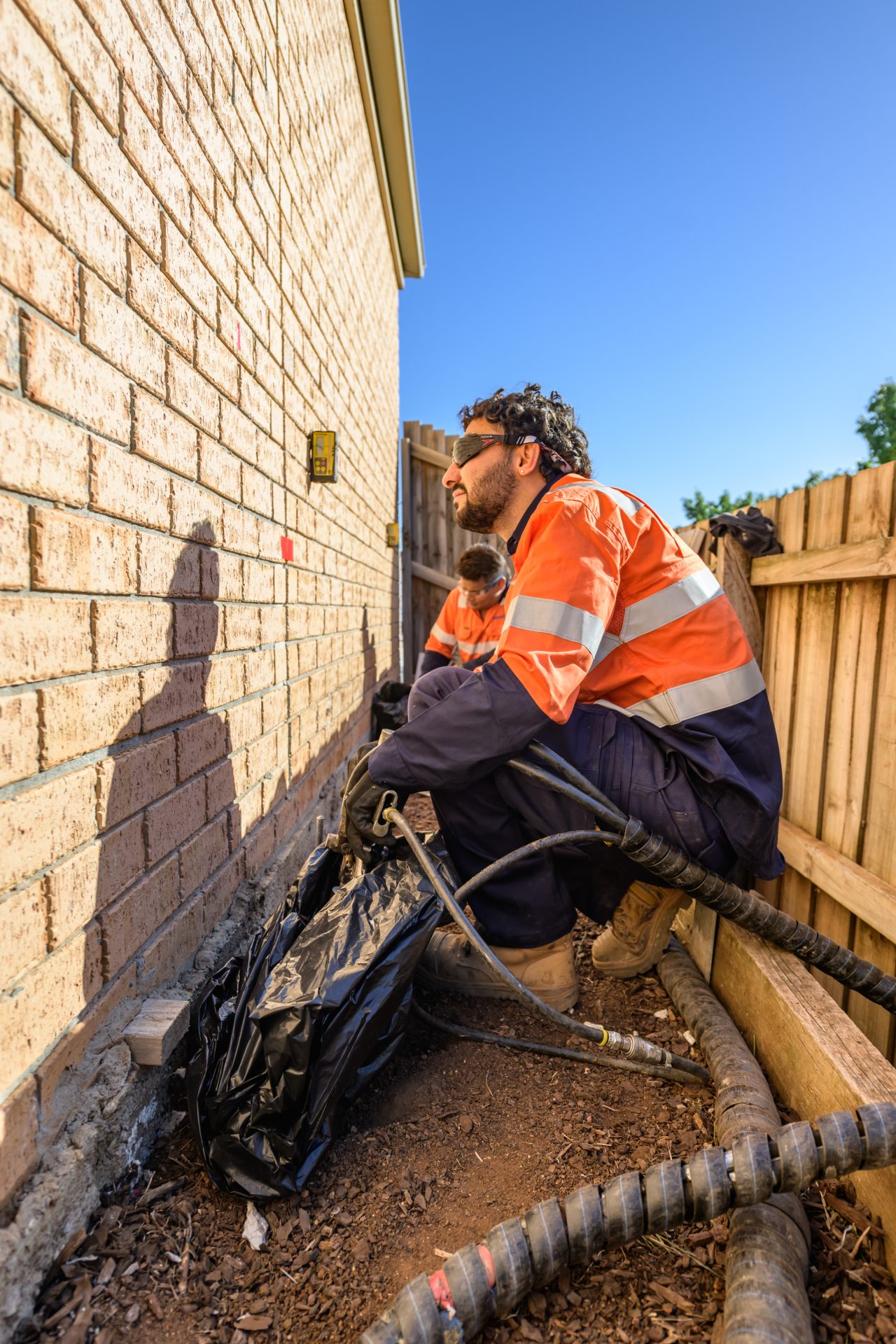
Resin Injection Underpinning
If a building is experiencing subsidence, a resin injection underpinning alternative is a fast and reliable solution that can save time and money compared to traditional underpinning.
With Mainmark’s Teretek® resin injection underpinning alternative, there’s no need for the excavation and digging associated with traditional underpinning. We drill small 16mm holes under the foundations of the building, and if required through the floor slab, and inject an inert resin formulation that fills voids, improves the soil, increases the ground’s load-bearing capacity and can also gently re-level the building or structure if required.
Our resin injection underpinning alternative is a durable and effective solution to many common causes of subsidence in commercial buildings, including:
- Soil shrinkage – Flooding or extended dry periods can deplete soil moisture, causing the soil under foundations to fail.
- Erosion – Wash out of fine material due to defective drains is just one of the examples.
- Heavy traffic – Local traffic can cause subsurface vibrations, leading to subsidence in nearby properties.
- Historical land use – Mining, fracking and other previous activities can play a role in subsidence issues.
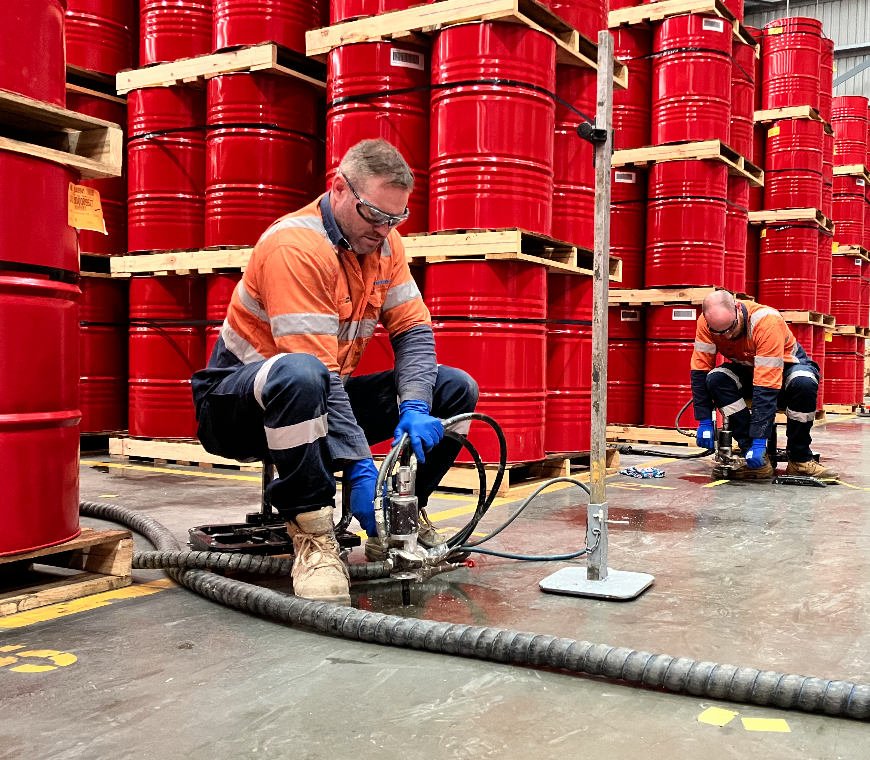
Teretek® Resin Injection
Our Teretek® resin injection underpinning alternative has successfully resolved subsidence issues for a wide range of applications.
We also offer JOG computer-controlled grouting, another option for overcoming subsidence.
Both solutions have been effective in projects from factories and offices to public buildings, heritage projects and retail centres. They are also suitable for residential homes.
Successful deployment in recent years includes rail and road networks and bridges, industrial plant, airport runways and other industrial buildings and infrastructure.
Resin injection Underpinning vs Traditional Underpinning
Traditional underpinning is a complicated and time-consuming process that involves digging out from under the foundations of a building and then adding piling or mass concrete. The process can take weeks or months to complete, and while work is carried out, the building must be unoccupied.
Mainmark’s Teretek® resin injection underpinning alternative simplifies the process so that commercial properties experience minimal downtime, protecting the businesses that use the buildings and property owners.
Our resin injection and computer-controlled grouting techniques are:
- Quick to implement – Work is usually completed within one or two days, and surfaces are immediately trafficable.
- Minimal disruption – Resin injection underpinning alternative treatment is carried out using surgical precision.
- Flexible – Our resin materials can be customised in terms of density, strength and flow rate to suit project requirements.
- Tidy and self-contained – While traditional can be messy and detrimental to landscaping, resin injection underpinning is a clean solution with minimal impact on the surrounding environment.
- Long-lasting and reliable – The resin is environmentally inert and remains in the ground to continue supporting the structure for many years.
House Underpinning
The traditional method
Excavation – Heavy machinery is required to dig large holes to depths often up to 3 metres.
|
Soil removal – large quantities of dirt and rock are loaded onto dump trucks and transported away from the site
|
Pouring Concrete– filling the holes or “piers” with concrete can be complex and logistically challenging depending on the site.
|
Curing time – concrete can take several days to get to strength.
|
House Resin Injection
The modern alternative
Tiny holes– Teretek is applied through keyholes, typically 6mm to 16mm in diameter.
|
Clean and quiet – The process is clean and quiet, has minimal impact on residents.
|
Resin injection – The resin injects into the ground and expands in the ground within minutes.
|
Curing time – 30 minutes. You can even use the building during the process.
|
Features & Benefits of Resin Injection Underpinning
Mainmark’s Solutions & Technologies For Concrete Underpinning
Fast
Our technologies have fast curing times and treated areas can be used immediately or without the delays compared to traditional repair methods.
Environmentally Inert
Our technologies use an inert material that is non-toxic and does not leach into the environment or affect the treated area.
Non-Invasive
Our solutions are of surgical nature compared to traditional methods.
Cost-Effective
Compared to traditional methods, our solutions are more cost-effective, with minimal disruption to the area.
© 2025 The Mainmark group of companies. ‘Mainmark®’, ‘Terefil®’, ‘Terefirm®’ and ‘Teretek®’ are trademarks of the Mainmark group of companies.
Mainmark Ground Engineering Pty Ltd
ABN: 51 606 182 503
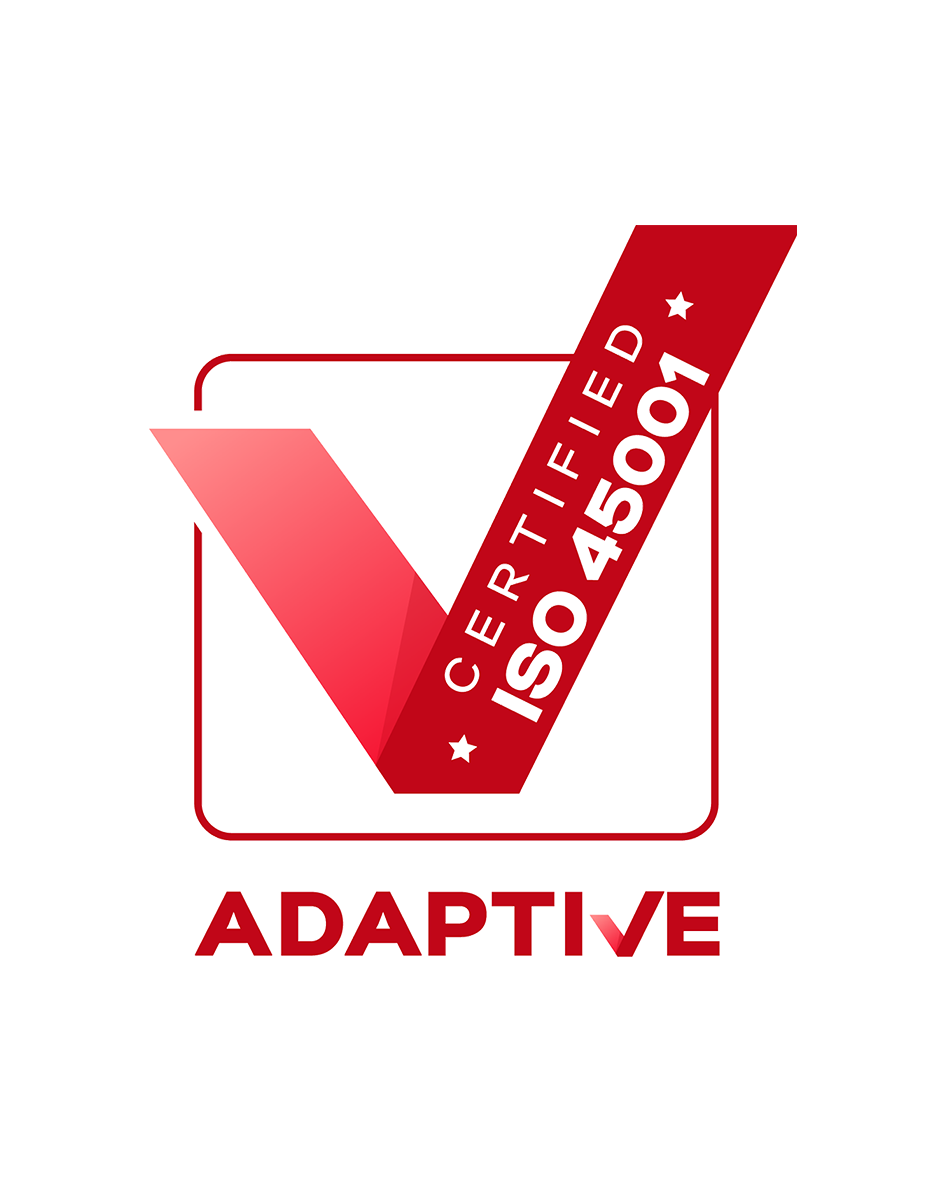
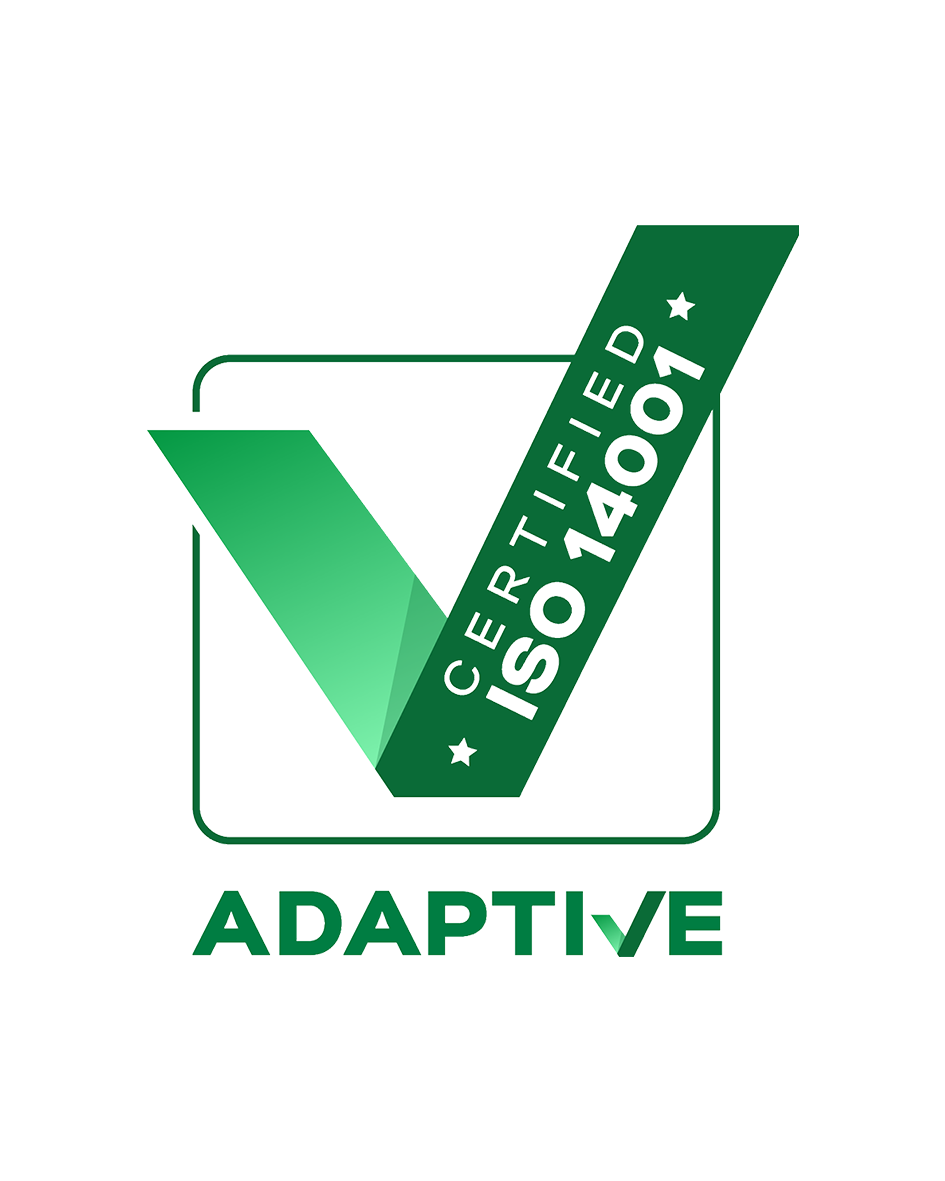
